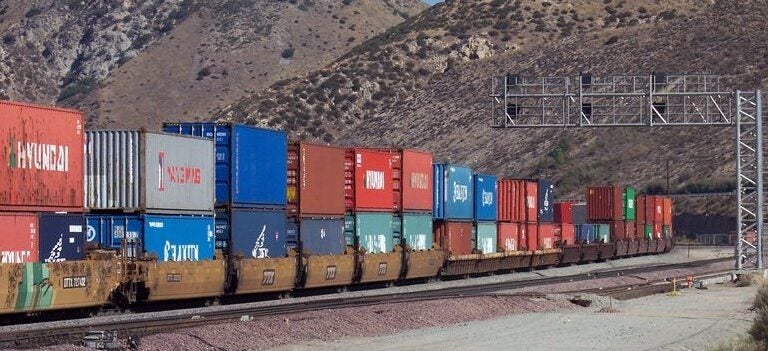
9. The Basics of Maritime Logistics
Author: Dr. James A. Fawcett, USC Sea Grant Maritime Policy Specialist/Extension Director (retired)
Media Contact: Leah Shore / lshore@usc.edu / (213)-740-1960
We’ve all seen the phrase, “Sorry, your item is on backorder.” Maybe you ordered a new copier and the manufacturer kept pushing back the delivery date. What did this message really mean? Where was the copier coming from? Let’s take a deeper look at the logistics chain of this copier to see what happened, its path to your office, and where it fit into the larger picture of distributing goods.
Manufacturing and Inspection Originates in China
It may have a U.S. name on it, but chances are it’s really made offshore, most likely in China. Yes, your copier came to life in Chongqing, Sichuan Province, and was packaged tightly and efficiently with 425 others in a 40-foot long ocean cargo container (as we described in Ship’s Log #2 of this series), to prevent damage on its long trip to Southern California. Joined by 150 other containers, it was loaded onto a railcar in Chongqing and the train arrived in the Port of Ningbo, China in a short 57 hours (it arrived much more rapidly than the former 12-day trip on a barge down the Yangtze River that occurred prior to 2018[1]). Upon arriving at Beilun Port in Ningbo, it is unloaded, inspected, and passed through Chinese customs on its way to a marshalling yard where it waited for the arrival of its ship (known as a “carrier”), for example, the CSCL Venus (14,000 TEU). Inspection in Ningbo also verified that the cargo identified on its bill of lading was correct. This is a description of who sent the cargo, the nature of the cargo, its route, and the identification of both the sender (known as the “shipper”) and the recipient, who is referred to as the “beneficial cargo owner” or BCO.
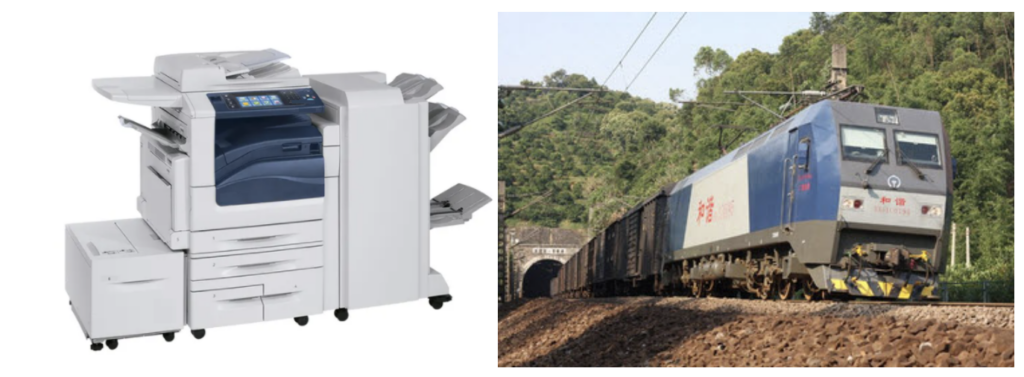
Post 9/11 Inspection Rule
After the 9/11 terrorist attack on the U.S., inspection, and certification is required of all cargo containers entering the U.S. that might pose a potential risk for terrorism[2]. Under the Container Security Initiative (CSI) implemented by the U.S. Customs and Border Protection (CBP) agency, a part of the Department of Homeland Security, those containers are inspected, at times, by U.S. agents stationed overseas at major foreign seaports.[3] In many cases, however, where the shipper is known and authenticated and has complied with the standards set by the Customs-Trade Partnership Against Terrorism (CTPAT), such as the company which made your copier, its cargo is considered low-risk because of that cooperation. This allows the cargo to avoid more stringent inspections under the CSI.[4]
The Cost of Shipping to Los Angeles
After waiting for a few days for the ship to arrive and another three days for it to discharge and embark cargo, your copier began its three-week voyage across the Pacific Ocean, arriving in Los Angeles 21 days later. The cost of that transit was paid by the manufacturer or shipper, and while rates change constantly depending upon the time of year, at the time of this blog publication, the trans-Pacific rate was approximately U.S. $4,027.[5] The charge for rail transit from Chongqing to Ningbo was an additional U.S. $169.
Upon arriving in Los Angeles, the bills of lading, which were carried onboard the vessel, were required to be electronically transmitted to the U.S. port of entry 96 hours prior to arrival. Containers coming from an unknown shipper that may have been approved at the port of departure are again subjected to non-invasive investigation (NII) at the port of entry. If CBP continues to have concerns after the NII, it may cause the container to be unloaded for detailed inspection. Since your copier was sent by a company that is a participant in the CTPAT Program, it was considered low-risk and its bill of lading passed through to the CBP inspector without intensive inspection. Following approval, duty was collected from the agent of the shipper before the container was released onto the next link in the logistics chain.
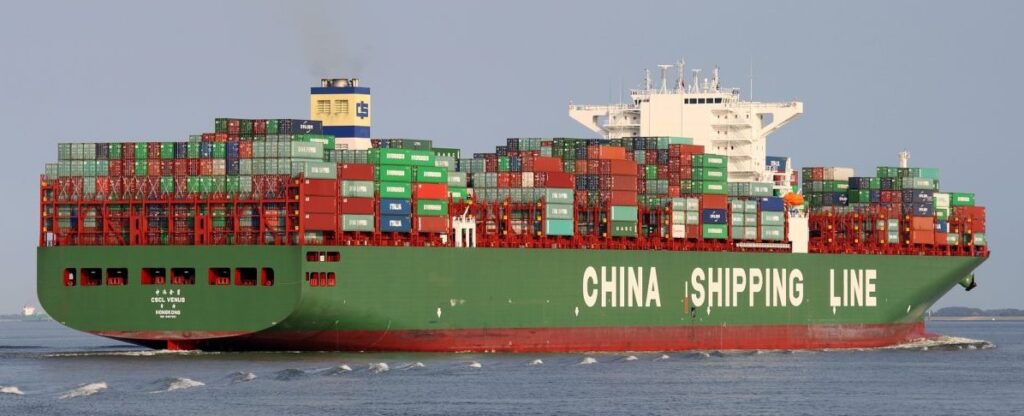
The Important Role of the Customs Broker
The role of the customs broker at the port of entry plays a very important role in coordinating the movement of cargo through the customs process and is critical to facilitating a smooth flow of cargo through it. The agent is also a communications link between the shipper, U.S. Customs and Border Protection, and the BCO, serving as a virtual midwife to each container for whom he/she is responsible. If legal issues arise over a container, the agent may also work with a law firm to resolve those issues.
Transportation Across the Western U.S.
Assuming that your copier shipment had no serious problems with customs, the container next moved to the terrestrial transport system. In earlier articles, I have mentioned that the rule of thumb for the Ports of Long Beach and Los Angeles is that cargo moving 500 miles or less to its final destination (e.g. Tucson, Phoenix, Las Vegas, San Diego, San Francisco, or Oakland) will probably travel by truck as we see on our freeways. Generally, for destinations further than that (e.g.Chicago, Houston or New Orleans), it will be loaded onto a freight train from one of two railroads that serve the Western U.S.: Burlington Northern Santa Fe (BNSF) or Union Pacific (UP). For our ports in Los Angeles County, that means that cargo is put onto a double-stack train where special railcars carry either two 40-foot containers stacked on top of each other, or a combination of a 40-foot container and two 20-foot containers. At a major transportation node, the train stops to unload containers and transfer them to a wheeled chassis in a configuration that looks somewhat like a semi-trailer (see Ship’s Log #2 for a description) for the next phase of transport. Since your copier was coming to a local retailer, it was delivered by truck either to a distribution center for chain retailers or directly to the retailer’s loading dock for your pick-up.
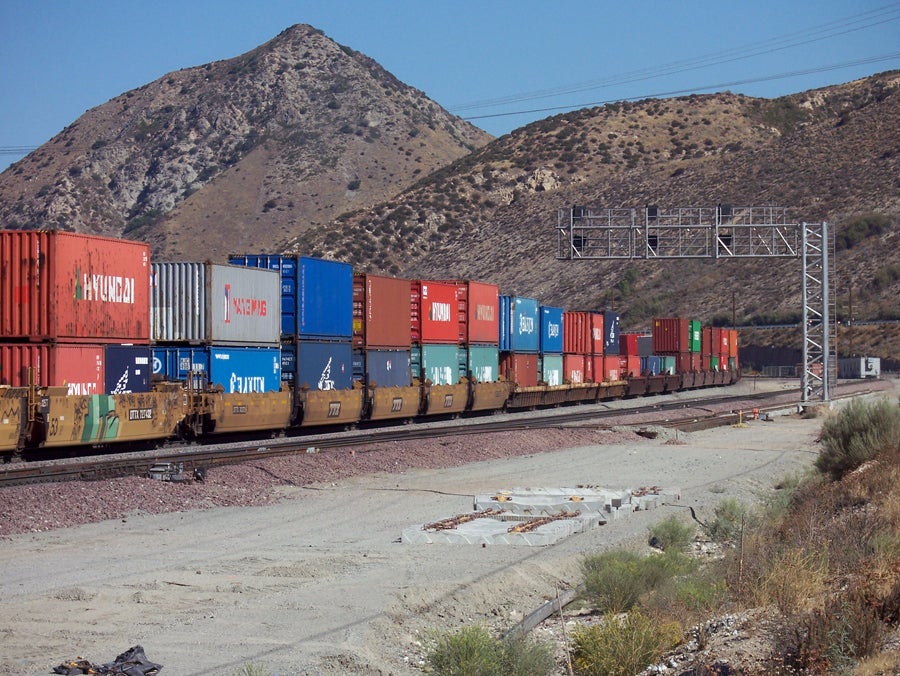
Routes for the Midwest and East Coast
However, if you are in the Midwest or the East, your copier most likely came through Chicago, the rail hub for the U.S. Historically, Chicago evolved into this role because in the 19th Century it was the second-largest U.S. city; it had both rail and water (through the Great Lakes system) and links to many of the major population centers in the country. In addition, the cost and legal arrangements (right-of-way costs) of establishing rail lines are substantial enough that once implemented, they rarely are abandoned. Thus, Chicago still is the central hub for much of the nation’s cargo. Moreover, a vast infrastructure surrounding the rail system in Chicago was developed and has supported its viability and permanence. If your copier was headed for the East Coast, once it got to Chicago, it likely was moved onto the tracks of one of the two major East Coast railroads: the CSX System or Norfolk Southern railroad. From there, the copier began its final destination to your doorstep.
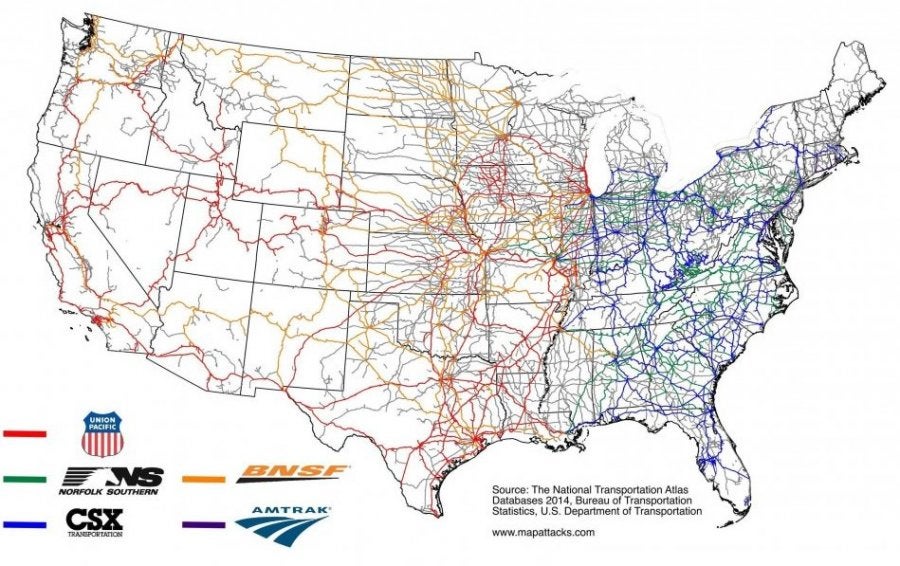
The Final Payment
When the copier arrived, no matter the location, it came with a copy of the bill of lading (to prove ownership). Further, the container was only released when appropriate payment was made to the agent or customs broker responsible for collecting fees owed for transportation, customs duty, and any other debts. Even if carriers offer door-to-door service, billing is not always comprehensive (i.e. each mode in the transport chain may bill separately).
Communication and Partnerships are Key to Shipping Success
As you might imagine, the maritime logistics system involves complex relationships between shippers, their transportation partners, government inspectors, a host of facilitators often known as agents or brokers, and firms known as “freight forwarders (also called “third-party logistics coordinators” or 3PLs). In addition to these relationships, the key to their smooth operation is a complex communications system to which they all share access. It is clearly a dance with many partners involved where communications and partner relationships allow your copier to be made in one country and delivered to another with amazing speed and reliability.
Note: Now that the key parts of the logistics system have been explained, next month’s article will discuss what happens when it is under stress from disruptions of various types including from adverse weather, to natural disasters, to labor disputes, to even merely the seasonal stresses that influence the speed with which cargo is moved from one overseas country to another. We will also explain the return route for containers delivering cargo from China/East Asia back to their point of origin
References
[1] Railway Pro. 25 Jan 2018. New Freight Rail Service Between Chongqing and Ningbo.
[2] Containers subject to inspection might have been from a new, unfamiliar or unusual shipper about whom there is little information or a shipper who has previously sent cargo that was detained or a shipper that U.S. Customs and Border Protection has reason to believe may be shipping banned or dangerous cargo.
[3] CSI: Container Security Initiative. ND. https://www.cbp.gov/border-security/ports-entry/cargo-security/csi/csi-brief.
[4] CTPAT: Customs Trade Partnership Against Terrorism. ND. https://www.cbp.gov/border-security/ports-entry/cargo-security/ctpat.
[5] Freightos Baltic Index (FBX): Global Container Freight Index. 12 Jan 2021. China East Asia to North America West Coast. https://fbx.freightos.com/.