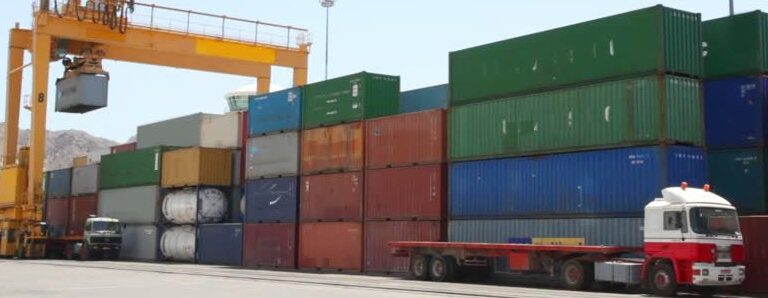
10. Does an Empty Have Value? The Demand for Containers in the Supply Chain
Author: Dr. James A. Fawcett, USC Sea Grant Maritime Policy Specialist/Extension Director (retired)
Media Contact: Leah Shore / lshore@usc.edu / (213)-740-1960
In the last blog post (see Ship’s Log #9), we learned about the journey that a manufactured product in China would take as it travels by rail, sea, and rail again from Chongqing to Chicago. It’s a long trip, but thanks to innovations in the goods movement, the mythical copier in the example was able to make the journey in a little more than 30 days, a feat not even imaginable 20 years ago. In this discussion, we’ll take a look at both a return trip for the 40-foot cargo container to China, as well as the delays and congestion that can occur in the supply chain as goods travel over this multimodal cargo system, especially last year under the shadow of COVID.
Leaving Chicago
Picking up where the journey ended, what happened in Chicago when our copier and its mates were unloaded? The container, which may be owned by the carrier or by a container leasing firm, loses money when it is idle. The shipper’s responsibility for the container ends when the shipment is delivered, so a brokerage firm takes it and tries to reassign it to a shipper with cargo bound for Asia to once again put it in use.
What cargo is moving from the U.S. to Asia? It will likely be some form of dry cargo, perhaps high-tech computerized milling equipment or an agricultural product such as almonds. Once filled, the container is sent in the reverse direction from Chicago to Long Beach to be carried on another container vessel such as the Orient Overseas Container Line (OOCL) M-Class ship M/V Chongqing (13,208 TEU)[1]. In this case, the third-party-logistics coordinator (3PL) was fortunate to find a westbound customer for the container, but in other scenarios, it might have headed in the other direction to Savannah or Charleston where OOCL serves Europe,[2] in which the container would then continue from Europe back to Asia. In a normal year, if it came to the West Coast via Long Beach, CA, the container would be back on the dock in Ningbo in about 60 days with intermediate stops in Busan and Shanghai[3]. However, due to “bunching” of cargo and voyages as a result of the COVID virus, the return trip for empty containers is now closer to 100 days.[4]
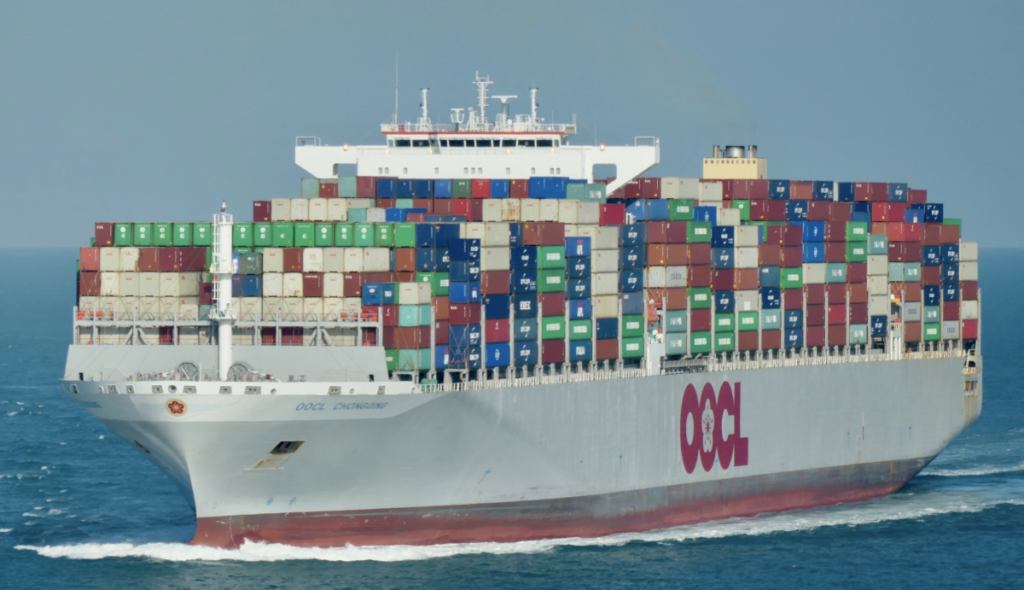
Empty Containers
The demand for containers is much greater in Asia, where many products are made, than in the U.S., where they are consumed. Thus, there is often a surplus of containers in America, and a high demand for them in Asia. Carriers would rather not backhaul empty containers, however since they are in high demand in Asia, in addition to the agricultural, technological, sophisticated products that we send, we will also sometimes fill empties with some products the U.S. commonly exports for recycling, such as bales of waste paper or plastic waste. Although the products are of low value, nevertheless they can be profitably recycled, especially when the cost of westbound transportation in the Pacific is very inexpensive. For example, the water-only rate for a 40-foot container from Long Beach to Ningbo could be as cheap as US$653[5], as compared to the same eastbound trip between the two ports at US$4,027.[6] If the system functioned smoothly—and that would mean that an equal volume of containerized goods is moving both eastbound and westbound—there would not be the dislocation of containers that we observe: i.e. a surplus of containers in the U.S. and a dearth of them in Asia.
COVID Complications
Keith Gaskin, Group Commercial Director of SEKO Logistics, a first-class logistics services provider, notes, “Social distancing due to COVID-19 is causing huge issues at the ports … It’s taking a lot longer, especially at Felixstowe [UK], to unload vessels. The ships are often leaving before the operators can load all the export and empty containers, as they don’t want to miss its next berthing spot [at the next port]. It’s a huge mess and is placing a huge strain all across the supply chain for carriers, port operators, forwarders, NVOs [non-vessel operating common carriers, also known as third party logistics coordinators][7], and the end-clients.”[8]
The nature of liner shipping places strict arrival-departure limits on vessels, much like airlines, such that operators must depart on time even if export cargo is left on the docks. Further, empty cargo containers are low-revenue loads for the carriers and low-priority for loading aboard a ship that is on a tight time schedule.
Quoted in the Journal of Commerce,[9] the authoritative voice of the shipping and goods movement industry, Rolf Habben Jansen, CEO of the carrier Hapag-Lloyd, says that increasing the inventory of available containers [by manufacturing new ones in Asia] will provide only limited relief to the international supply chains. Some Asian carriers are so eager for containers that they have discussed vastly increasing fabrication of new containers despite the cost. But Jansen’s point is reinforced by Alan Murphy of Sea-Intelligence ApS in Copenhagen, who reported in a recent webcast[10] that it would not be possible over the short term to fabricate sufficient new containers in time to relieve the current shortage in Asia.
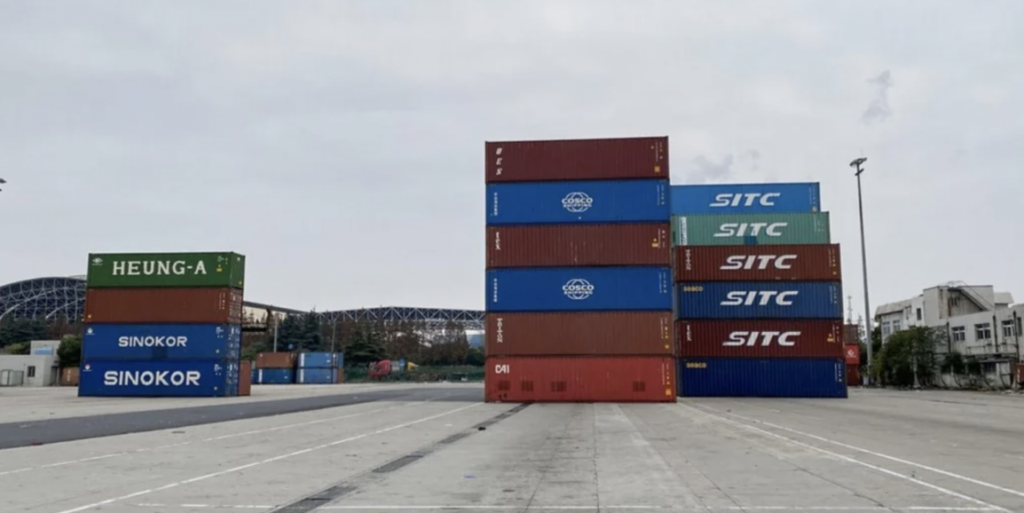
A Snowball Effect from the Beginning of COVID
The fundamental problem with dislocation of available containers is described by Lars Jensen, also featured in the Journal of Commerce,[11] who explains that the entire supply chain was disrupted by the COVID virus and the sudden slowdown in demand in the second quarter of 2020. When demand dried up, carriers responded by reducing voyages and port calls, resulting in stranded empty containers in North America. Suddenly, in the fourth quarter, demand increased for Asian supplied goods but the supply of containers there had not been renewed by westbound vessel sailings from North America.
As Joe Wallace, who wrote in the Wall Street Journal, explained, “Ocean freight rates began to soar last summer, and haven’t let up. That is partly because consumers, unable to spend money in restaurants, have splashed out on goods that move by sea.”[12] Thus, the competition for available containers and cargo slots on the available ships increased the prices charged for space—both container and vessel capacity—and the carriers sought to respond by adding surcharges to published rates as well as adding delays to the availability of vessel space. The demand in Asia for containers continues as a surfeit of empties in North America languishes.
Other Slowing Effects of COVID
However, the influence of the virus continues to affect the supply chain both at sea and on land. Containers stranded in the U.S., Canada, and Mexico are not merely the result of inadequate sailings to Asia. Slowed unloading at distribution centers, slowed deliveries by truck, slowed movement of containers off receiving port terminals, and slowed clearances through U.S. Customs are all consequences of the impact on the labor pool from COVID illnesses and added safety precautions. What has historically been about a 60 day cycle for returning containers to Asia is now commonly acknowledged to be more than 100 days, as has been noted by Ms. Xie (above).
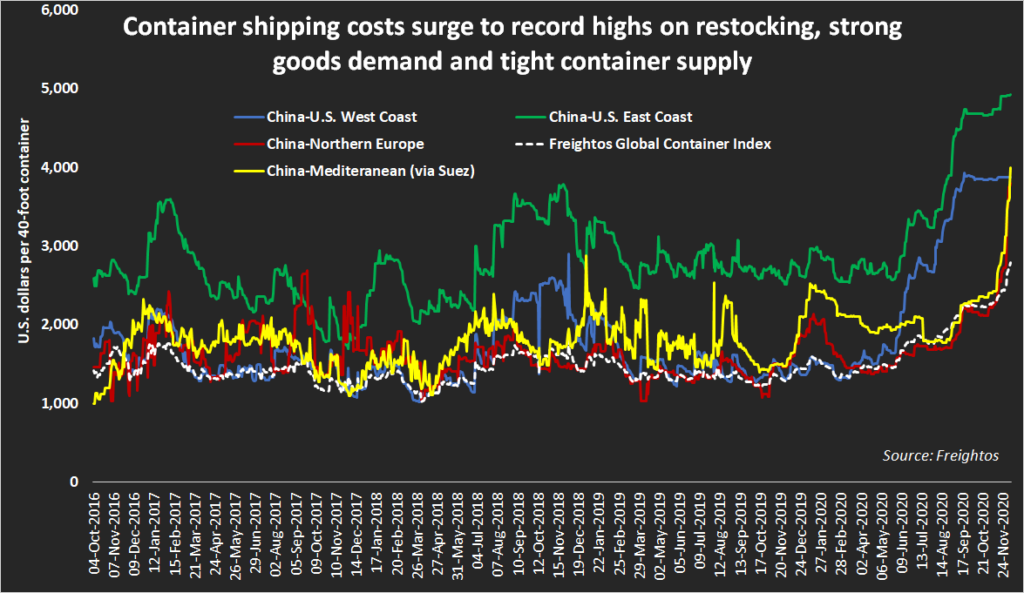
When Will the Container Disequilibrium Resolve?
It will take time for the container shortage to resolve. The supply chain is now operating in overdrive. It is responding to demands not only for imports to North America but also to demand from Asian customers for delayed exports from manufacturers on this side of the Pacific. So, carriers returning to Asia are loaded with export cargo and since that export cargo is prioritized by U.S./Canadian/Mexican shippers, it will take priority over moving empty boxes to Asia. We do not know how long the supply chain will struggle with this dilemma but voices in the industry, such as Alan Murphy and Bill Mongeluzzo, have advised that it will probably take months to see the supply chain recover into something approaching equilibrium. If the system became unbalanced because of an unanticipated pandemic that is expected to take months to resolve, it is probably wise to heed their experienced advice.
How Does This Affect You and Me?
Now that we’ve been quarantined at home for almost a year, we’ve found all sorts of home improvements that have demanded our attention. We have been increasing the demand for furniture, electronic goods, and other home improvement products made in Asia—that’s what is inside many of those imported shipping containers.
In Ship’ Log #9, we considered the route and timing for a copier made in China to reach a destination near Chicago in a normal year, and it is pretty amazing how quickly that can happen. However, now we have seen how the supply chain is affected not only by demand but also by labor shortages due to illness. At least for empty containers, it takes almost 70% more time for the container to complete that circuit from China, to us, and back to China. The system will eventually rebalance as the U.S. economy recovers, especially when the demand for Asian-produced products becomes satisfied. According to the industry, though, it will take months for that to happen, and the rate of recovery is likely to track with U.S. workers returning to a more normal work schedule. We can probably expect delays in goods coming from Asia of up to double of what would happen in recent years. If there is one consolation to all this, it is that if we’re unhappy that our anticipated copier is delayed, so is its manufacturer. The COVID virus has been an equal opportunity disrupter on both ends of the supply chain.
References
[1] OOCL. (n.d.). OOCL Services: Our Vessels. https://www.oocl.com/eng/ourservices/vessels/Pages/default.aspx.
[2] OOCL. (n.d.). Atlantic Product and Service Guide, 2020. http://ebook.oocl.com/transatlantic_tat2/mobile/index.html#p=1
[3] OOCL. (n.d.). Pacific Product and Service Guide, 2020. http://ebook.oocl.com/tpt_day4/mobile/index.html#p=6
[4] Xie, S.Y. (24 Jan 2021). China Export Rise Faces Jam. Wall Street Journal, p. A9.
[5] FBX. (14 Jan 2021). Freightos Baltic Index (FBX): Global Container Freight Index. https://fbx.freightos.com/
[6] These figures fluctuate weekly and do not account for surcharges that carriers may place on them due to shortages of containers, thus demand, which can at times double published rates.
[7] Companies that have ongoing relationships with carriers; they accept cargo for transit from shippers and coordinate the documentation to its destination. They are not carriers but coordinate between shippers and carriers, especially on irregular shipments of goods.
[8] Knowler, G. (09 Nov 2020). Box Shortage Tightens on Europe-Asia Volume Growth. Journal of Commerce. https://www.joc.com/maritime-news/box-shortage-tightens-asia-europe-volume-growth_20201109.html.
[9] [Unattributed]. 15 Feb 2021. More containers can’t solve shortage. Journal of Commerce, p. 6.
[10] Murphy, A. (04 Feb 2021). Container Shipping Outlook: Analyzing the Trans-Pacific (webcast sponsored by the Journal of Commerce).
[11] Jensen, L. (21 Feb 2021). Two sides of the same coin. Journal of Commerce, p. 52.
[12] Wallace, J. (19 Feb 2021). Container shortages drive up commodities. Wall Street Journal, B1.